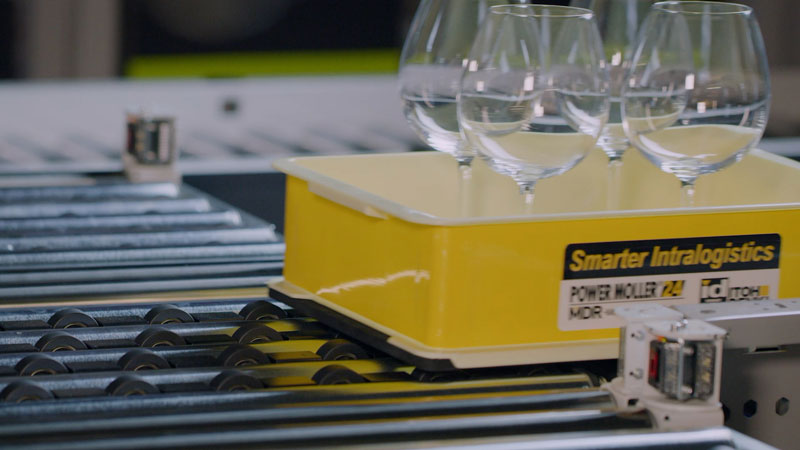
It’s often said that speed is of the essence. And while that’s certainly true in modern processing, warehousing and e-logistics facilities, facing requirements for ever quicker throughput, just as important is product safety.
Handling fragile or sensitive products – safely and effectively – is a challenge that has faced system designers and manufacturers for many years. Items ranging from cartons of fresh eggs and glass bottles, to sensitive electronical parts and chemicals, need to progress through the facility without the risk of damage that will mar their value and potentially damage equipment, resulting in costly downtime.
In these applications, products simply cannot be subjected to sharp lateral movements, sudden drops or stops, or impacts from other products or equipment.
These challenges have been considered by our research & development teams for many years and our current technology portfolio now addresses each of them to provide a safe and reliable solution across a broad spectrum of applications.
Fast movements or jolts – in any direction – have just as much potential to cause damage to products as collisions. It is vital that any movement is smooth, precise and controlled.
Controlling the position of loads, and the distance between them, is essential to avoid the risk of impacts. To achieve that efficiently, MDR conveyor lines are based on short, independent conveyor zones. Drawing on information received from sensors located in each zone, they can continually adjust stops and starts with appropriate accelerations and decelerations to ensure the smoothest possible movement.
Another very challenging area is lateral diversion of items, where the requirement to maintain throughput while keeping initial costs down has often meant recourse to pneumatic or high-power technologies.
However, due to their lack of precision, and the possibility of impacts to diverted loads, these solutions have proved to be unfit for the handling of fragile loads – and indeed generally for users seeking to protect the condition of their items for quality reasons.
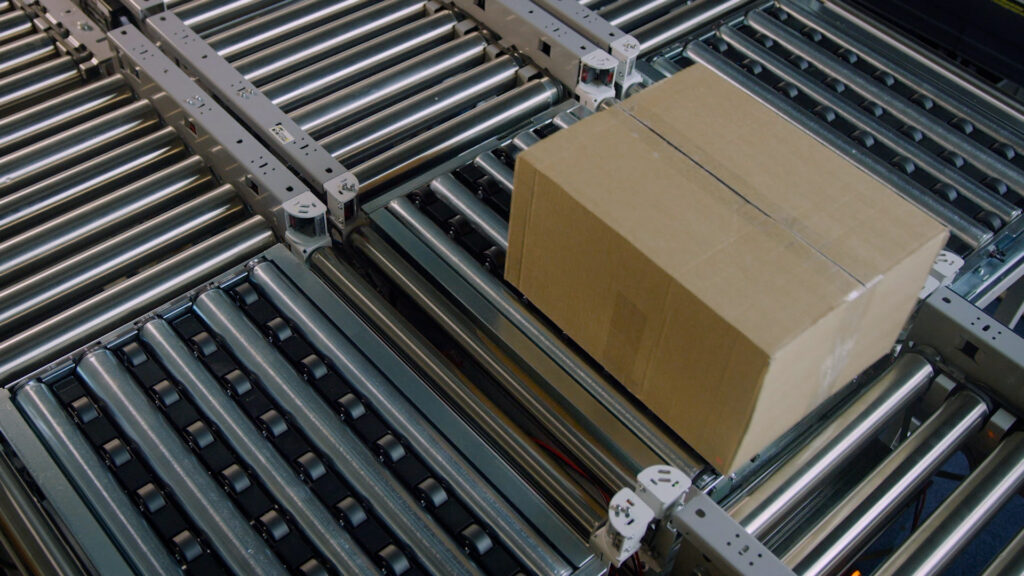
To meet these challenges, Itoh Denki has developed a range of compact lateral diverters based on MDR technology. Using precise mechanical sequences and controls with no impact and no elevation of loads, these diverters deliver smooth transfers while keeping up with challenging throughput requirements.
In many facilities, items have travel up or down gradients. In these instances, boxes or items must not collide with each other or fall off the conveyor due to increasing speeds. The use of servo-driven magnetic brakes is key here to ensure control over the speed of the loads and to maintain distance between them.
Furthermore, in the event of a power shortage or sudden power issue, an optional mechanical braking system integrated into the motor roller drives can be used to block the rollers where the product is on an incline or decline, bringing the system to an immediate and complete stop.
It is these attributes of Itoh Denki systems which are seeing them specified for fragile applications as varied as the conveying of glass bottles of whisky and even the processing of eggs into boxes.
To find out more about how our systems could assist in your application, get in touch: https://itoh-denki.com/contact/