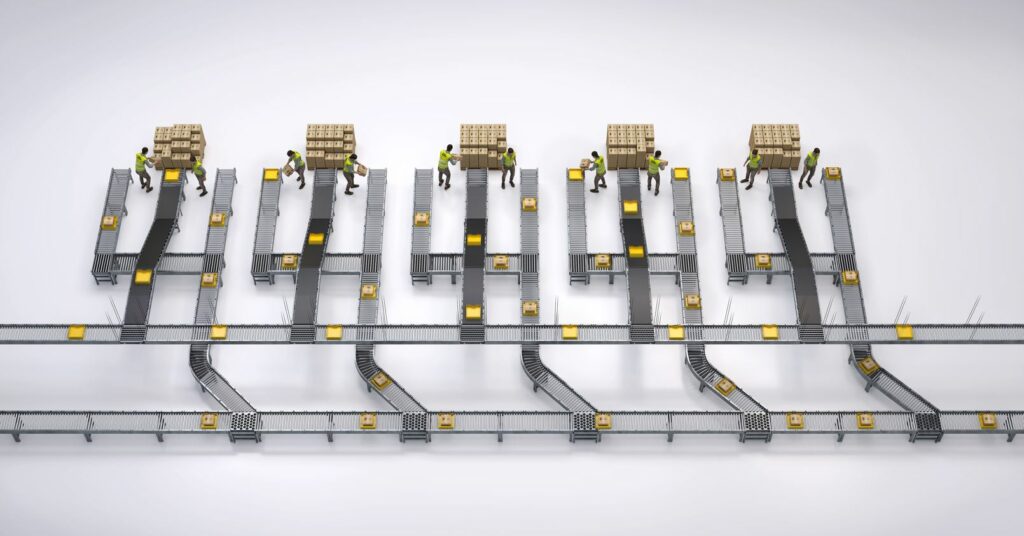
The need to smoothly and rapidly route products onto and off conveyor lines is a key challenge which has to be met to ensure optimal efficiency across a broad spectrum of logistics processes.
In both fulfilment and distribution centres, sortation is a critical process, playing a variety of roles from routing products exiting automated storage and retrieval systems (ASRS) to order preparation stations, to the sorting of parcels by destination ahead of shipping.
A variety of technologies are available to handle sortation tasks, each with its own particular attributes.
This means careful consideration must be given to selecting the best solution to ensure optimal process efficiency and flexibility, while avoiding unnecessary complexity and excessive cost.
Specifiers must take into account factors such as the size, shape, weight and fragility of the items to be sorted; the available space; the number of sorting locations; and the required throughput.
This last point is key given that the demands on many fulfilment facilities are growing, leading system designers to seek ways to make better use of space rather than the cost of moving operations elsewhere.
These instances often see the installation of multi-layer conveyors, each layer requiring its own sortation system to remove and reintroduce products to the line.
To deal with all of these sortation challenges, Itoh Denki offers a range of compact and modular diverters, all driven by the same efficient 24Vdc technologies which form the heart of our renowned motor-driven roller (MDR) systems.
As a result, sortation lines incorporating these systems are completely modular and readily reconfigurable or expandable to suit changing operational requirements.
Furthermore, control and maintenance are simple and can be handled in-house in the vast majority of applications.
For 90° transfers, our F-RAT modules can smoothly divert up to 2,250 totes/ hour, each with a maximum weight of 50kg.
Meanwhile, our POP-UP diverters offer a straightforward and economical solution for sortation at 30° or 45° to either the left or right.
For sortation and merging operations requiring relatively high throughputs, our MABS modules can be integrated to serve 30°, 45° and 90° exits, diverting up to 4,300 cases/hour, each weighing up to 30kg. This makes the MABS the ideal solution to solve bottlenecks at traffic-intensive points on lines, while FRAT and POPUPS could be used at less throughput-intensive points to optimise the cost of the solution even further.
All of our diverters guarantee smooth diverts, efficiently working with ZPA (zero pressure accumulation) controls, This eliminates the risk of impacts and shocks and so offering smooth and secure sortation in a broad range of low to medium-high throughputs. It also makes them ideal for processes handling fragile and sensitive parts.
Itoh Denki diverters provide complete flexibility in conveyor design, allowing for rapid modification or expansion to adapt to evolving requirements, across both single and multi-layer conveying systems, especially when compared with very high throughput heavy installations which are typically more complex to control, less flexible and unsuited to multi-layer applications.
You can find out more about our diverter and sortation solutions at https://itoh-denki.com/products/diverter-and-sortation-modules/