La sécurité est toujours une considération essentielle lorsque des personnes doivent travailler à proximité d’un équipement en mouvement. Cela ce traduit ainsi par des réglementations locales et internationales strictes. Aussi, pour assurer le plus haut degré de qualité et la satisfaction du client, il est primordial de garantir l’intégrité des produits traités tout au long de la ligne de manutention.
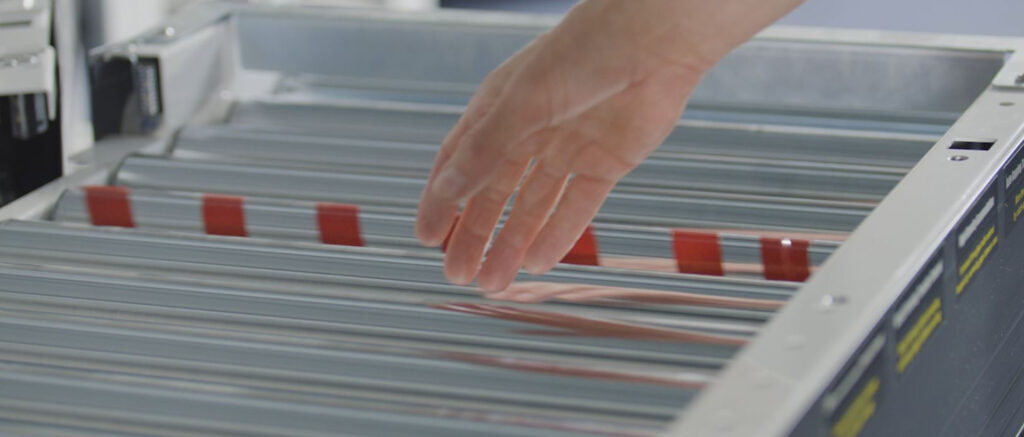
Assurer la sécurité et la conformité réglementaire des systèmes de convoyage
Les fabricants de produits de l’UE, ainsi que les concepteurs, les installateurs et les intégrateurs de systèmes, doivent respecter les normes CE qui régissent tout, des risques mécaniques et électriques aux risques d’interférences électroniques, en passant par les risques liés au mouvement des équipements.
La création de systèmes de convoyage sûrs doit être envisagée dès le stade de la conception du système.
De nombreux convoyeurs traditionnels utilisent des moteurs de 400 V pour entraîner de grandes longueurs de convoyeur, souvent à l’aide de longs axes et de poulies rondes, ou de chaînes et de pignons pour les charges plus lourdes.
Pour assurer sa fonction, le convoyeur nécessite alors une puissance importante, augmentant ainsi le niveau de risque et la nécessité de mettre en place des mesures de sécurité couteuses et contraignantes.
De plus en plus de convoyeurs modernes sont basés sur des rouleaux motorisés et sont divisés en sections modulaires beaucoup plus petites, chacune avec son propre petit moteur. Cela permet de diviser la puissance nécessaire pour convoyer un produit, de sorte que le risque de blessure est bien moindre, si une main ou un doigt venait à entrer en contact avec le convoyeur.
Le mécanisme du convoyeur lui-même est également plus sûr, avec des poulies en caoutchouc reliant chaque rouleau à son voisin. Les avantages en matière de sécurité sont considérables, tandis que la nécessité et le coût des protections supplémentaires sont supprimés.
Ce type de système est aujourd’hui courant pour les petites charges, mais les versions plus grandes peuvent désormais traiter des charges allant jusqu’à 1 tonne, ce qui signifie qu’elles peuvent être utilisées sur des lignes de convoyage de palettes.
L’absence de système de transmission complexe et l’utilisation de courant 24VCC permet aussi de réduire les risques encouru lors des opérations d’entretien.
Les défis en matière de sécurité dans les opérations de tri
Les progrès en matière de sécurité ont également été significatifs dans les systèmes de déviation et de tri sur les lignes de convoyeur. Les systèmes pneumatiques ou à courant alternatif ont souvent été le choix privilégié pendant de nombreuses années. Cependant, ces systèmes posent des problèmes de sécurité importants en raison de la puissance élevée et des espaces non protégés entre les pièces mobiles. Ils génèrent également des niveaux de bruit élevés au détriment des opérateurs qui travaillent à proximité toute la journée.
Parmi les solutions de déviation les plus courantes, les bras à commande pneumatique qui poussent le produit vers une sortie unique. La pression et les forces pneumatiques élevées entraînent un risque de blessure grave si un opérateur entre en contact avec le produit en fonctionnement. Les barrières et les grilles peuvent atténuer le risque, mais cela représente un coût et ajoute de la complexité à la conception de la ligne.
Itoh Denki a récemment introduit le MABS, une nouvelle génération de module de déviation modulaire, utilisant de petites roues multidirectionnelles qui peuvent dévier les charges en toute sécurité à n’importe quel angle, éliminant ainsi le besoin de pousseurs pneumatiques, avec l’absence de compresseur bruyant et les problèmes de maintenance et de sécurité.
Ces systèmes sont alimentés par un courant continu de 24 V, plutôt que par un courant triphasé de 400 V, ce qui nécessite un câblage et une mise à la terre importants, ainsi qu’une maintenance spécialisée, coûteuse et plus régulière, entraînant généralement la fermeture complète de la ligne.
Ces déviateurs alimentés en 24V DC et ces rouleaux motorisés peuvent simplement être remplacés en cas de besoin, l’entretien de routine étant assuré par un opérateur interne.
Il est essentiel d’éviter les chocs et les collisions pour minimiser les dommages causés aux charges. Il est primordial de maintenir la distance entre les charges individuelles, ce qui est particulièrement important lorsque les caisses montent ou descendent des pentes. C’est notamment le cas en cas de coupure de courant ou de nécessité d’arrêter la ligne.
Les freins magnétiques servomotorisés remédient à ce problème en continuant à fonctionner même en cas de coupure de courant. Les systèmes de freinage mécanique peuvent également arrêter la ligne lorsque le produit est en pente ou en déclin.
La prévention des dommages aux marchandises
Les avantages des solutions 24VDC d’Itoh Denki en matière de sécurité pour les opérateurs s’étendent également aux autres produits ; des solutions telles que les bras de poussée représenteraient un sérieux défi lors du transfert de charges fragiles ou provoqueraient des blocages réguliers. Cependant, les déviateurs 24VDC comme le MABS ou le F-RAT sont conçus pour convoyer les produits en douceur, en maintenant toujours un espace entre les colis et en déviant sans changement de niveau entre l’entrée et la sortie, ce qui élimine le risque d’endommagement du produit.
Tous ces facteurs doivent être pris en compte dès les premières étapes de la conception du système, afin de s’assurer que les personnes et les produits ne subissent aucun dommage résultant du processus de manutention et que les marchandises sont acheminées de manière fiable et sûre jusqu’à leur destination finale.