Wenn es um die Förderung geht, ist jede Anwendung anders.
Die Länge der Förderbereiche; das Vorhandensein von Biegungen, Neigungen und Gefällen; die Art, das Gewicht, die Größe und die Form der gehandhabten Produkte: Dies sind nur einige der Faktoren, die Systemdesigner auf der Suche nach einer optimalen Lösung berücksichtigen müssen.
In vielen Fällen entscheiden sich die Planer für Förderbänder. Dies ist typischerweise der Fall, wenn Herausforderungen in Bezug auf die Haftung bestehen, insbesondere wenn Neigungen oder Gefälle in das System integriert werden müssen; und um kleinere, ungewöhnlich geformte, weiche oder zerbrechliche Produkte mit unterschiedlichen Formen oder Größen zu bewegen.
Aus diesen Gründen sind Förderbänder sehr häufig in Einrichtungen zu sehen, die von Postdiensten betrieben werden oder Aufträge für E-Commerce-Unternehmen erfüllen.
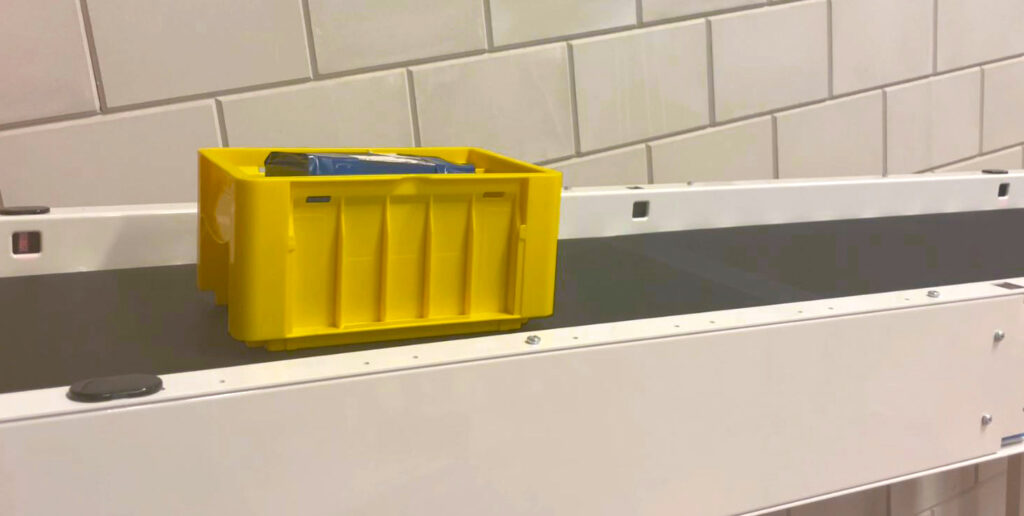
Beim Entwurf eines Förderband-Systems können Planer typischerweise zwischen Förderern mit externem AC-Antrieb und Förderern mit motorisierten DC-Antriebsrollen (MDRs) wählen. MDR-angetriebene Förderbänder werden oft durch Laufen des Bandes auf zahlreichen Rollen entwickelt, um einen sogenannten „Band auf Rolle“- oder „Band über Rolle“-Förderer (BOR) zu schaffen.
Die endgültige Wahl kann von zahlreichen Faktoren bestimmt werden, aber MDRs werden aus einer Reihe von Gründen immer häufiger für diese Anwendungen eingesetzt.
Erstens führt der Einsatz modularer MDR-Technologien dazu, dass die Förderstrecke in kürzere, unabhängig gesteuerte Abschnitte zerlegt wird. Dies ermöglicht eine bessere Kontrolle des gesamten Produktflusses durch die Linie.
Der modulare Charakter von MDR-basierten Systemen und die Einfachheit des Fördererdesigns haben auch eine erheblich leichtere Wartung zur Folge. Bei Bedarf können einzelne Abschnitte schnell und einfach gewartet werden und Aufgaben wie Rollen- oder Riemenwechsel können von einem hauseigenen Techniker übernommen werden, ohne dass auf externe Unterstützung gewartet werden muss, was eine minimale Betriebsunterbrechung bedeutet.
Das Zerlegen des Förderers in kürzere, mit 24 V DC betriebene Abschnitte und der Betrieb der Riemen auf Rollen ermöglichen eine geringere Riemenspannung und Reibung, was im Vergleich zu herkömmlichen Riemenförderern mit externem 400 V-Antrieb zu einer deutlich besseren Energieeffizienz führt.
Die Unterteilung des Förderers in Abschnitte bedeutet auch, dass das Drehmoment an einem bestimmten Punkt der Linie geringer ist, wodurch das potenzielle Verletzungsrisiko für Bediener, die am System arbeiten, verringert wird.
Der vielleicht größte Vorteil von MDRs für Menschen, die den ganzen Tag an Fördersystemen arbeiten, ist die Lärmreduzierung. Diese Eigenschaft wird zunehmend zu einem Faktor bei der Entscheidungsfindung bei größeren Unternehmen, die ihren Mitarbeitenden ein ruhigeres Arbeitsumfeld bieten möchten.
Die PM605KT-Rolle von Itoh Denki eignet sich besonders gut für BOR-Anwendungen – dank ihrer starken Widerstandsfähigkeit gegen hohe Spannungen und ihrer für einen 24-VDC-Motor konkurrenzlosen Leistung. Dieser Motor ermöglicht es, Lasten von bis zu 1.000 kg zu bewältigen.
Das System ist auch mit einer optionalen mechanischen Bremse erhältlich, die den Rollen- und Riemenabschnitt im Falle eines Stromausfalls oder eines Notstopps automatisch blockiert. Dies verhindert ein Loslösen und Abstürzen von Fördergütern, insbesondere an Neigungen, Gefällen oder hängenden Förderstrecken und sorgt so für eine sichere Anlage.
Je nach Anwendung können auch andere MDR-Lösungen geeignet sein – weitere Informationen finden Sie auf unserer Website: https://itoh-denki.com/de/produkte/antriebsmotorrollen-controller/