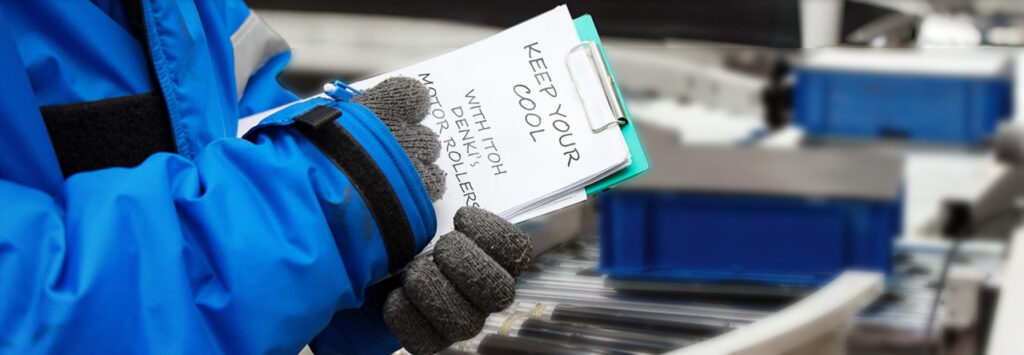
The use of cold storage is burgeoning rapidly. Cold storage is widely employed in the food & beverage manufacturing and distribution sector, but also increasingly in warehouses used by e-grocery businesses for storage and shipping to the immediate locality.
Another rapidly expanding area of coldroom usage is in the pharmaceutical sector where drugs need to be stored at a certain temperature in order to retain their efficacy.
Typical temperatures in these applications range from 0°C to -30°C which presents additional challenges for equipment operating in these environments, over and above what would be found in purely ambient conditions.
In particular, conveyor systems must be able to both start up and then operate consistently even at the very lowest end of this temperature range.
Any motors in use must be able to maintain stable torque and power output without overheating to the point that the temperature in the coldroom would be impacted. Stable external temperature on a motor is also important to minimise the build-up of condensation, which could corrode the motor and other system components if left unchecked.
Drive belts must also be able to maintain the correct operating tension and friction while delivering the required service life with consistent performance at these low temperatures. Frost build-up is a constant issue which can cause a loss of traction if the correct product is not specified.
As well as the equipment itself, the correct products must also be selected when it comes to maintenance. In the case of conveyors, this applies particularly to the lubricating products applied to components. These products must maintain optimal viscosity and lubricating performance when machinery is starting up in such low temperatures.
As well as the coldroom itself, careful consideration must also be given when specifying systems and products for use in ‘transition’ areas – where products exit the coldroom and find themselves, however briefly, in an area of ambient temperature before leaving the facility.
Once again, in these instances, the risk of condensation is a very real one and in many instances, specifiers need to select IP65 water-resistant products which are typically made from stainless steel and so offer strong resistance to moisture build-up.
Happily for specifiers, all of these challenges are amply met by Itoh Denki’s acclaimed motorises driver roller (MDR) line-up which boasts a number of products specifically designed for extended use in coldrooms.
The PM500FE and PM605FE can between them cope with loads of up to 500kg and feature a high-specification, external controller. For those preferring an internal control mechanism, the PM500XP has the circuit board and gear-motor integrated within the roller and can be easily controlled by PLC, Asi-Bus via Bihl & Wiedemann module, or logic sensors with integrated ZPA. For further information visit: https://itoh-denki.com/products/motorized-rollers/protection/cold-store/