Handling around 6 Million items of mail each day is only made possible by the high levels of automation and control integration. Mail is initially scanned and coded to identify product, item size etc and is then conveyed to the correct sortation area. Addresses are ‘read’ automatically by scanners powered by Siemens-designed computers that use 4.2million lines of code!
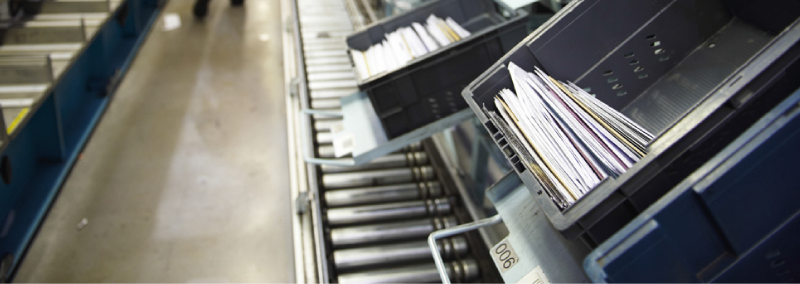
Letters and ‘flats’ are automatically batched by destination into trays ready to be conveyed to their appropriate destination. These trays are transported around approximately 4 kilometres of motorised roller conveyor driven by efficient Itoh Denki motorised rollers.
Power Moller® 24v drive rollers incorporate brushless technology that provides high levels of torque within a compact 50mm diameter roller. The drives are each controlled by a simple and flexible CB016 controller which provides commutation to drive the motor as well as several options for control by external PLCs.
Itoh Denki’s modular and compact drive solution not only reduces space requirements, they also reduce noise levels and energy consumption compared to traditional external drive solutions. The roller conveyor is made up of lots of drive zones that comprise of a single motorised roller and several slave rollers. In this way a drive zone is able to readily transfer the trays from one zone to the next. Because each zone is independently controlled the motors can be operated on a run-on-demand basis enabling substantial energy savings to be made compared with continuously running external drives with complex belt drives and pneumatic actuators or slipping clutches.
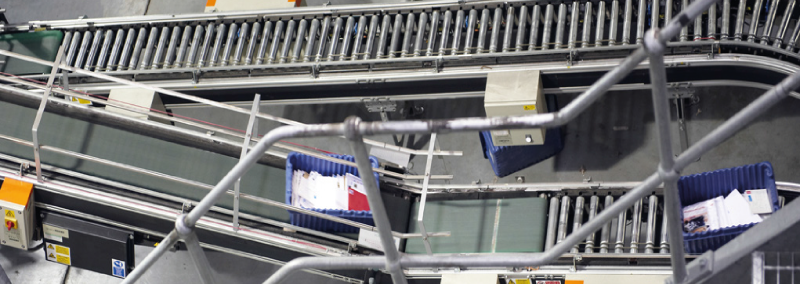
Calculations show that when comparing a similar section of conveyor driven by a continuously run external motor, Power Moller® drives can reduce energy consumption by up to 60%. The whole-life-costs of the installation are also affected by belt drives and clutches that often require replacement as little as two years after installation. With a typical life expectancy of around 20,000 hrs Itoh Denki motorised rollers are being selected by system integrators and end users as the preferred solution to unit conveying applications.