The need to safely, rapidly and effectively transfer product between processing areas is a well-established one across material handling functions in both manufacturing and logistics.
The challenge of efficienlty transfering heavier items
For smaller and lighter product, specifiers can select from a range of modular and easily commissioned options.
However, when it comes to larger and heavier items, the choices have traditionally been more limited.
But this requirement is growing, especially in sectors such as automotive where items such as electric vehicle batteries, as well as other larger components, must be transferred or routed between different processes.
System designers must also consider evolving operational requirements and how systems may need to be reconfigured to meet them.
Here, the ability to quickly rearrange process layout can be a significant advantage.
Weather it is in a production or in a logistic process, choosing the right diverter solution is crucial to ensure continuous and effective processing – and allay concerns around safety.
Compact, reliable and safe diverter based on Motorised drive rollers
While Motorised drive roller (MDR) based diverter technologies have become a technology of choice for precisely diverting smaller loads. However, for loads weighing more than 50kg, options have been more limited.
Common solutions have been relying on pneumatic systems or bulky chain driven mechanisms, which are among the few system types able to handle these bulkier loads.
Meanwhile, most electrical systems for these applications have generally required 400V three-phase power. This requires extensive cabling and earthing, as well as specialist, expensive and more regular maintenance, possibly resulting in complete line closure, as well as posing safety concerns.
In production or assembly processes, larger components which may often remain fragile during the production process and can’t be subjected to sudden shocks or impacts – even though they may undergo several phases of processing before leaving the facility.
However, an effective alternative does now exist in the form of our M-RAT technology.
M-RAT allay all the safety concerns of pneumatically powered systems, while offering precise transfers in a compact and flexible cassette design – drastically reducing costs associated with configuration and maintenance.
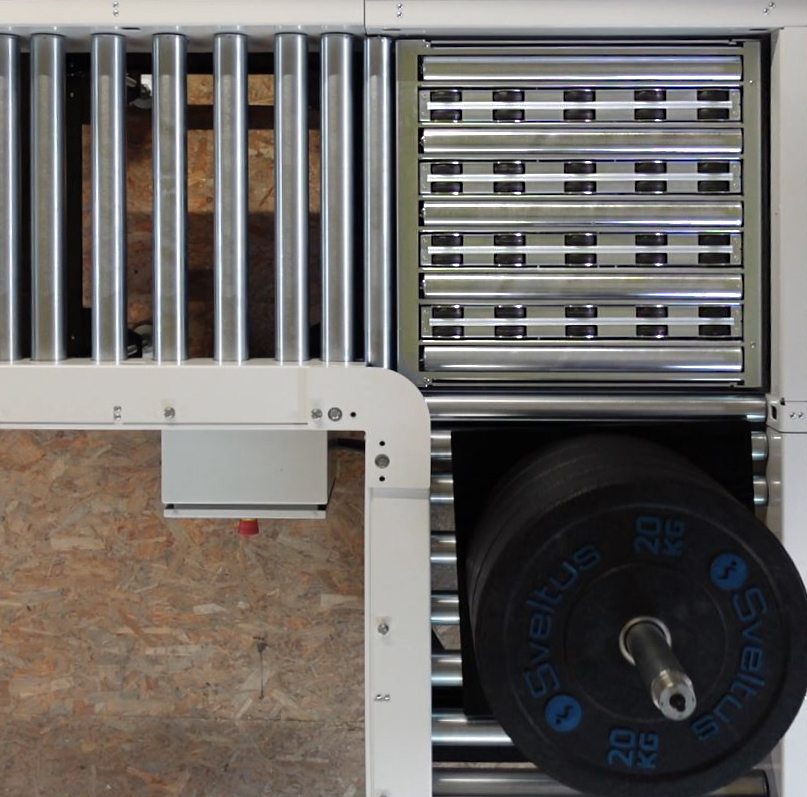
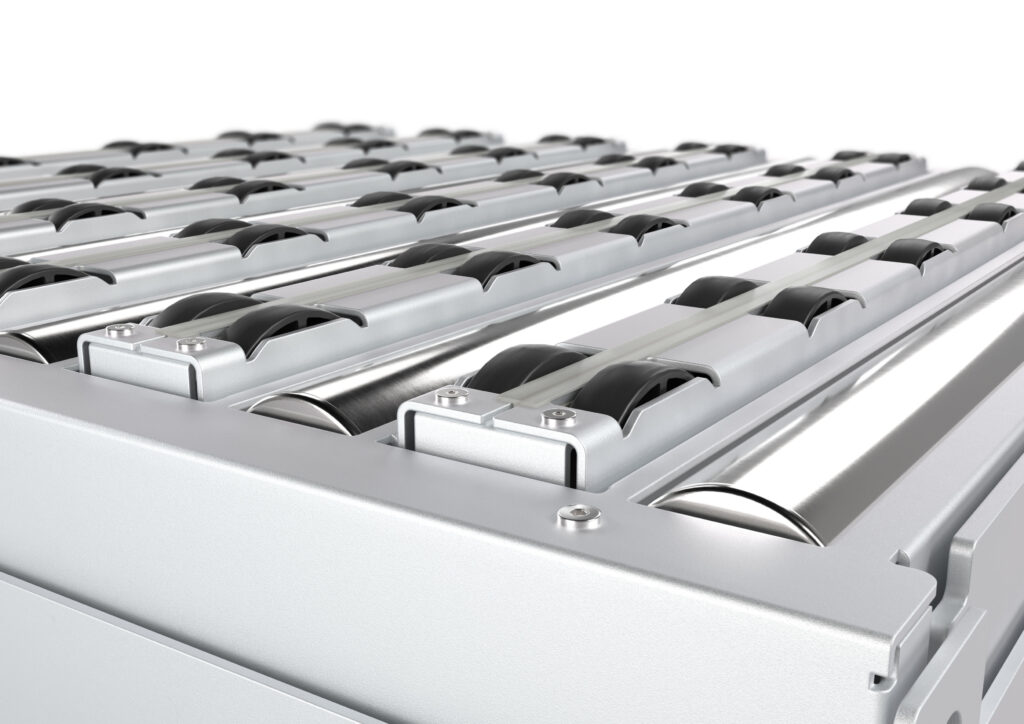
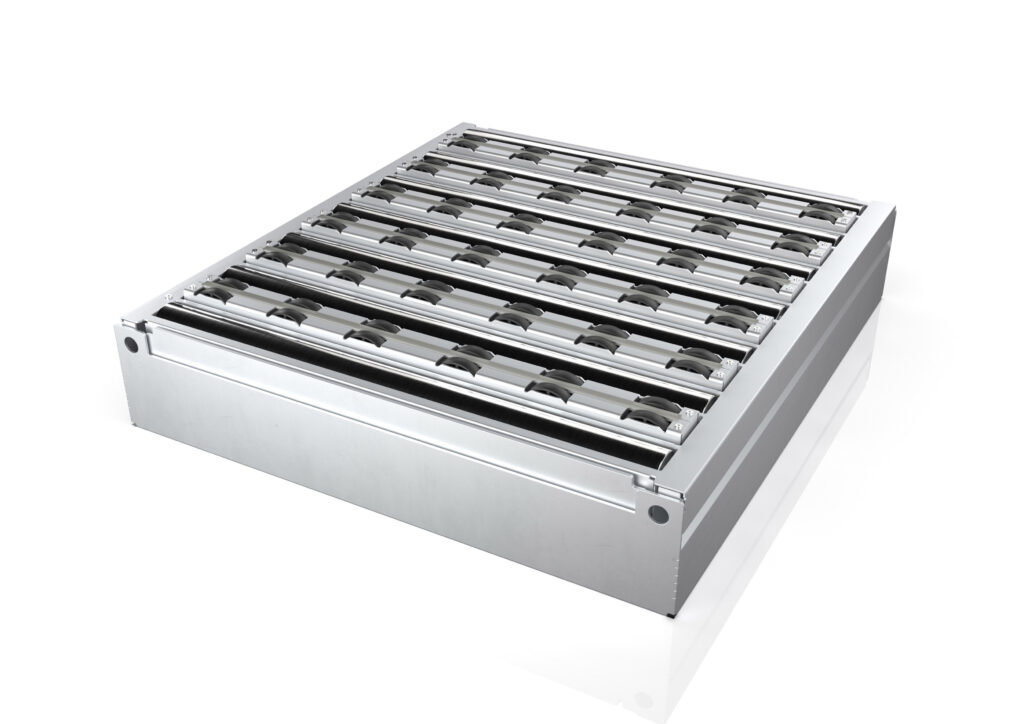
Drawing on our 24V DC powered F-RAT systems technologies which are proven in smaller load handling, the compact M-RAT modules can handle individual items weighing up to 250kg – giving far greater options for specifiers.
M-RAT is also much safer given thanks to its fully protected surfaces, and can simply be swapped in and out when needed, with routine maintenance such as belt or motor replacement undertaken by an in-house operative with no need for specialist external support.
Importantly, the use of 24VDC power means no need for 400V three-phase power, or pneumatic or hydraulic systems with all the associated installation, maintenance and high energy costs.
Diverting in cold rooms
A further benefit of M-RAT is that it can function effectively at temperatures as low as -30°C, making it ideal for routing cartons and products in frozen storage intralogistics operations.
M-RAT is already seeing significant take-up from specifiers and system designers who enjoy greater options and flexibility as well as the peace of mind knowing both colleagues and products are as safe as they can be.
For more information on the M-RAT consult the product page or contact us.